SURVIVAL THROUGH QUALITY
PRODUCT CENTER
-
Pulse dust collector
-
Mine dust collector
-
Boiler dust collector
-
Metallurgical dust collector
-
Carbon plant dust collector
-
Chemical dust collector
-
Rubber dust collector
-
Woodworking dust collector
-
Single machine dust collector
-
Static electricity Dust collector
-
Cyclone dust collector
-
Wet dust collector
-
Filter cartridge dust collector
-
Insert valve (gate valve)
-
Ventilation butterfly valve (cold air valve)
-
Spiral conveyor (auger)
-
Scraper conveyor
-
Dust humidifier
-
Bucket elevator
-
Ash discharge valve
-
Material Handling Equipment
-
Wet scrubber
-
Dust collector
-
Dust removal filter bag
-
Dust removal bag cage
-
Polishing platform
-
Waste gas treatment equipment
-
Electric control cabinet
-
Fan
-
Smoke welding machine
-
Liquid level switch
-
Dust removal filter element
-
Aeration cushion
-
Sweeper
-
Dust suppression device
-
Solenoid valve
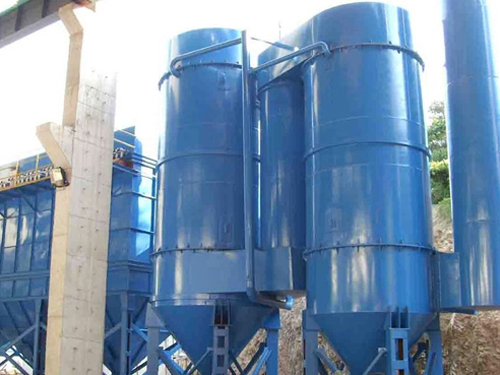
XNT-XST Wet Desulfurization Dust Collector
The XNT/XST wet desulfurization dust collector is a comprehensive device that integrates dust removal, desulfurization, self discharge or mechanical ash discharge, and automatic control of water replenishment. It has the advantages of easy operation and management, circulation of solution inside the dust collector, low water consumption, and economical operation.
The XNT/XST wet desulfurization and dust collector is treated with TO resin, a new achievement of the Chinese Academy of Sciences. The shell is built with metal or ceramic plates and a mixed structure of metal and ceramic. Its service life is comparable to that of a stone dust collector in terms of technology and economy.
XNT/XST wet desulfurization dust collectors are widely used in industries such as metallurgy, mining, power generation, and heating. They have high dust removal and desulfurization effects on coal-fired boilers, rolling track kilns and flat kilns in the ceramic industry, vertical kilns and dryers in the cement industry, inverted flame kilns for refractory materials, roasting kilns, smelting furnaces, and power plant boilers, especially for coal powder, liquefied beds, industrial boilers, heating boilers, and industrial kilns.
XNT/XST wet desulfurization dust collector is a popular type of dust collector in wet impulse dust collectors. Water bath dust collector has a simple structure, low cost, and is easy to maintain and manage. This type has been in operation for fifteen years, which fully proves its stability and can be constructed with bricks or concrete according to local conditions. It is suitable for flue gas purification and desulfurization of smaller capacity boilers.
In order to improve desulfurization efficiency, further technical modifications were made to the nozzle design, which incorporated two fluid induced swirling mechanisms to ensure the formation of filmization and condensation, and further improved the dust removal and desulfurization efficiency through bubbling. This product has achieved success. XNT and XST wet cyclone agglomeration desulfurization and dust removers are desulfurization equipment with low pressure loss and dust removal capability. They are mainly composed of cylinder, spray device, sieve plate, dehydration and demisting device, overflow hole, cleaning hole, etc. The working principle is that smoke containing dust and sulfur oxides enters the cylinder through the flue, and the alkaline absorbent solution containing [OH -] ions is sprayed out from the upper, middle, and lower parts of the bubble desulfurization and dust removal equipment through spiral nozzles, forming multiple rows of high-speed atomization water curtains that are opposite to the smoke. This increases the probability of collision between smoke, dust, sulfur oxides, and water, and fully utilizes the speed of atomization droplets to create a high gas-liquid relative velocity, achieving the dust removal and desulfurization effects of a single dust collector.
Dust removal mechanism of XNT/XST wet desulfurization dust collector:
The smoke enters the water surface inside the nozzle to stimulate, and the coarse dust particles are captured and settled by the water due to inertial collision, which is the flushing stage; The jet nozzle gap swirls at a high speed to stimulate a large number of bubbles and water spray swirling along the cylinder, resulting in the filmization and condensation of smoke and dust. Bubbles continue to occur and break, forming a strong swirling disturbance. Smoke and dust are constantly washed and absorbed at the edge of the cylinder to settle, forming a foam action stage; The airflow passes through the foam layer and enters the aroused spray and fog drop area, which is washed by the shower, and the smoke is further absorbed and purified, that is, the action of the shower is interrupted; When the smoke containing mist droplets rises to the conical dewatering plate, it is intercepted and flows down the wall, serving as the fourth stage of both dehydration and dust removal. The entire process of dust removal and desulfurization is unified, with sufficient water liquid absorbent for SO2 gas. The contact between bubbles and water mist completes the desulfurization effect.
Design principles for XNT/XST wet desulfurization and dust collector:
1. Not forcing the shutdown of the ash discharge machine to cause production losses.
2. Can be used in conjunction with desulfurization.
3. The maintenance cycle is long and suitable for the maintenance period of the boiler unit.
4. Economically energy-saving, low water and electricity consumption.
model | Boiler capacity t/h | ||||||
2 | 4 | 6 | 8 | 10 | 15 | 20 | |
Air volume range m3/h | 4600-6000 | 9000-11000 | 10000-13500 | 16000-22000 | 24000-28000 | 33000-37500 | 46000-54000 |
Total dust removal efficiency% | 95-98 | ||||||
Desulfurization efficiency% | 75-80 | ||||||
Resistance Pa | 600-800 | ||||||
Ringman blackness | <1 | ||||||
Segmented particle size uM | <1 | ||||||
Water consumption I/m3 | 0.10-0.30 |
Technical performance of XNT wet desulfurization and dust collector:
model | Smoke volume m3/h | Dust removal efficiency% | Smoke emission concentration (mg/Nm3) | Ringman blackness (Level) | Desulfurization rate (%) | Resistance (Pa) |
XNT-2 | 4500~6000 | 95-99 | <100 | <1 | 75-85 | 1000-1500 |
XNT-4 | 9000-11000 | |||||
XNT-6 | 15000-16000 | |||||
XNT-8 | 19000-21000 | |||||
XNT-10 | 23000-26000 | |||||
XNT-15 | 34500-39000 | |||||
XNT-20 | 46000-52000 | |||||
XNT-35 | 85000-92000 | |||||
XNT-40 | 92000-115000 | |||||
XNT-65 | 150000-190000 |