SURVIVAL THROUGH QUALITY
PRODUCT CENTER
-
Pulse dust collector
-
Mine dust collector
-
Boiler dust collector
-
Metallurgical dust collector
-
Carbon plant dust collector
-
Chemical dust collector
-
Rubber dust collector
-
Woodworking dust collector
-
Single machine dust collector
-
Static electricity Dust collector
-
Cyclone dust collector
-
Wet dust collector
-
Filter cartridge dust collector
-
Insert valve (gate valve)
-
Ventilation butterfly valve (cold air valve)
-
Spiral conveyor (auger)
-
Scraper conveyor
-
Dust humidifier
-
Bucket elevator
-
Ash discharge valve
-
Material Handling Equipment
-
Wet scrubber
-
Dust collector
-
Dust removal filter bag
-
Dust removal bag cage
-
Polishing platform
-
Waste gas treatment equipment
-
Electric control cabinet
-
Fan
-
Smoke welding machine
-
Liquid level switch
-
Dust removal filter element
-
Aeration cushion
-
Sweeper
-
Dust suppression device
-
Solenoid valve
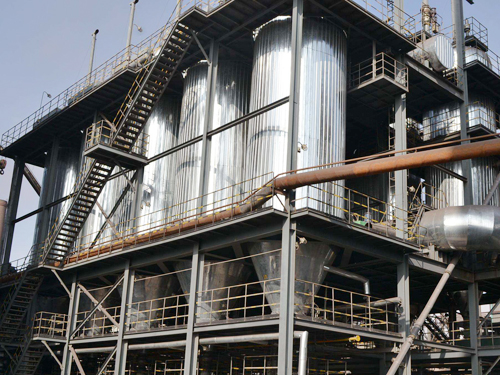
Steel blast furnace gas dust collector
The steel blast furnace gas dust collector adopts the technology of chamber stop pulse injection dust cleaning, which overcomes the shortcomings of conventional pulse dust collectors and chamber backflow dust collectors. The dust cleaning, dust removal, low emission concentration, low air leakage rate, low energy consumption, low steel consumption, small footprint, stable operation, and good economic benefits. Suitable for the purification of dusty gases and material recovery in industries such as metallurgy, building materials, cement, machinery, chemical engineering, power, and light industry.
The steel blast furnace gas dust collector is composed of raw gas (260 ℃) from the main pipe of raw gas, which enters the lower box of the bag type dust collector through a branch pipe. After mechanical separation, the gas is filtered upwards through a cloth bag, and fine dust adheres to the outer surface of the filter bag. The clean gas is collected into the upper box through the filter bag, passes through the clean gas branch pipe, and is used in hot blast furnaces during the main pipe. After filtering for a certain amount of time, as the dust on the surface of the filter bag increases, the resistance of the dust collector increases. When the resistance reaches a certain value, the electrical control system sends out a cleaning signal, and the pneumatic disc valve and upper ball valve of the outlet branch pipe automatically close. The pulse valve opens, and nitrogen gas from the cylinder is sprayed into the bag mouth through the blowing pipe, causing the filter bag to expand.
The dust on the outer surface of the filter bag is shaken off and falls into the lower conical ash hopper. At the end, a pulse valve is sprayed and the dust collector continues to remain stationary, causing the finer dust in the cylinder to settle in a static state. This process is completed, and the pneumatic butterfly valve and upper ball valve of the outlet branch pipe are opened. The dust collector enters the normal filtering state. At the same time, the lower ball valve opens and passes through the impeller feeder, completing the dust cleaning process of the box. The opening and closing of each valve and the testing of dust concentration in a single box are controlled by the PLC system. This cycle of work is to purify the raw gas.