SURVIVAL THROUGH QUALITY
PRODUCT CENTER
-
Pulse dust collector
-
Mine dust collector
-
Boiler dust collector
-
Metallurgical dust collector
-
Carbon plant dust collector
-
Chemical dust collector
-
Rubber dust collector
-
Woodworking dust collector
-
Single machine dust collector
-
Static electricity Dust collector
-
Cyclone dust collector
-
Wet dust collector
-
Filter cartridge dust collector
-
Insert valve (gate valve)
-
Ventilation butterfly valve (cold air valve)
-
Spiral conveyor (auger)
-
Scraper conveyor
-
Dust humidifier
-
Bucket elevator
-
Ash discharge valve
-
Material Handling Equipment
-
Wet scrubber
-
Dust collector
-
Dust removal filter bag
-
Dust removal bag cage
-
Polishing platform
-
Waste gas treatment equipment
-
Electric control cabinet
-
Fan
-
Smoke welding machine
-
Liquid level switch
-
Dust removal filter element
-
Aeration cushion
-
Sweeper
-
Dust suppression device
-
Solenoid valve
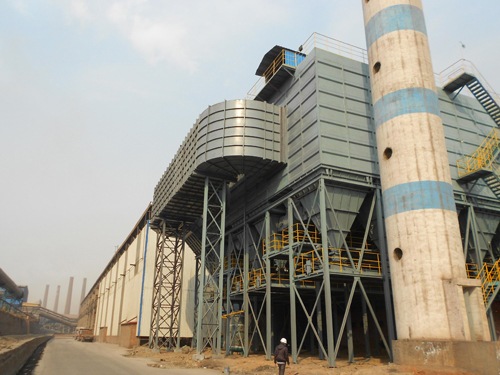
Steel plant dust collector
The steel plant dust collector uses a filter bag made of porous filter cloth to separate dust particles from the flue gas flow. During work, smoke flows through the filter bag from the outside to the inside, and dust particles are blocked outside the filter bag.
The steel industry is a major contributor to atmospheric pollution, and the management of exhaust gases in the steel industry follows the principles of comprehensive management. Striving to reduce energy consumption and raw material consumption is one of the fundamental ways to increase exhaust emissions; Innovate processes, adopt processes and equipment to increase the emission of waste gases from consumer processes; Adopting energy-saving management methods and equipment, as well as managing and recovering exhaust gas; Vigorously promote comprehensive use.
At present, the sintering machines of large steel plants in China will emit a large amount of smoke during the sintering process, which will contain substances such as nitrogen, sulfur dioxide, dioxins, and dust. Taking the 280 square meter sintering machine as an example, the substance discharged into the atmosphere contains a dust concentration of 150mg/Nm3. Based on this calculation, it will cause great pollution to the environment. Currently, China has formulated detailed requirements and standards for energy conservation and emission reduction, continuously improving environmental protection regulations, and placing high demands on environmental protection. According to the current standards in China, the dust concentration discharged into the atmosphere is less than 50mg/Nm3, and the bag filter device is an important link to achieve this requirement.
Main structure of steel plant dust collector:
1. The dust collector is divided into 24 compartments and arranged in two rows, with the main air ducts for inlet and outlet in the middle. The compartments are tightly separated by partitions to achieve offline ash cleaning.
2. A wind deflector is installed between the air inlet of each compartment and the filter bag, and the air inlet method is taken inside the box.
3. Each warehouse is equipped with manual butterfly valves, and the outlet is equipped with pneumatic stop valves. It can achieve offline ash cleaning and the maintenance of individual compartments and the distribution of air volume for each compartment without stopping the dust collector.
4. Each warehouse is equipped with 216 filter bags, with a size of 120mm x 6000mm. There are a total of 5184 warehouses with a total filtration area of 11716m2.
5. The filter bag frame adopts an octagonal star shaped cross-section. Compared with a circular cross-section, it can enhance the cleaning effect, reduce wear between the filter bag and the frame, help extend the service life of the filter bag, and facilitate the extraction and insertion of the filter bag frame.
6. The filter bag material is made of polyester needle punched felt.
7. Adopting the method of stopping wind and pulse cleaning, each compartment is equipped with a set of spraying device, and the spraying pipe and pulse valve outlet are connected in a plug-in way for easy disassembly and assembly.
8. The electromagnetic pulse valve is a DMF80 straight through pulse valve, and its pressure output port is a double twisted wire structure.
9. The top of the upper box is equipped with a drainage slope (20:1) and a drainage channel to prevent water accumulation on the top cover.
11. Each warehouse is equipped with an ash hopper, a warehouse wall vibrator, and a manhole door.
12. The lower opening of the ash hopper is equipped with a manual plug valve and a star shaped ash discharge valve, the former for inspection and repair of the star shaped unloader.