SURVIVAL THROUGH QUALITY
PRODUCT CENTER
-
Pulse dust collector
-
Mine dust collector
-
Boiler dust collector
-
Metallurgical dust collector
-
Carbon plant dust collector
-
Chemical dust collector
-
Rubber dust collector
-
Woodworking dust collector
-
Single machine dust collector
-
Static electricity Dust collector
-
Cyclone dust collector
-
Wet dust collector
-
Filter cartridge dust collector
-
Insert valve (gate valve)
-
Ventilation butterfly valve (cold air valve)
-
Spiral conveyor (auger)
-
Scraper conveyor
-
Dust humidifier
-
Bucket elevator
-
Ash discharge valve
-
Material Handling Equipment
-
Wet scrubber
-
Dust collector
-
Dust removal filter bag
-
Dust removal bag cage
-
Polishing platform
-
Waste gas treatment equipment
-
Electric control cabinet
-
Fan
-
Smoke welding machine
-
Liquid level switch
-
Dust removal filter element
-
Aeration cushion
-
Sweeper
-
Dust suppression device
-
Solenoid valve
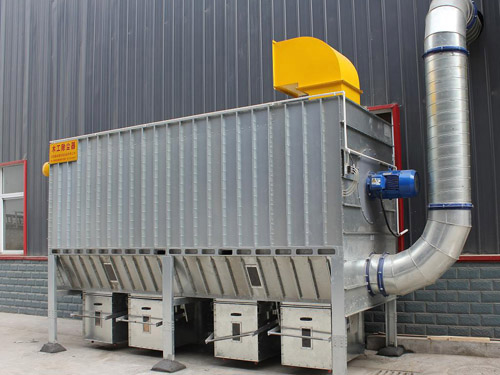
Woodworking dust removal system
The woodworking dust removal system is based on the principle of saving investment as much as possible. Due to the high concentration of dust generated by woodworking equipment during the processing, the commonly used pulse bag dust removal technology in China is adopted to achieve the goal of recovering dust and purifying exhaust gas, so that all emission indicators meet the emission requirements.
There are two important technical and economic indicators for the process of woodworking dust removal system: investment cost and operating cost. The former is one-time, while the latter is regular, and its cumulative amount can be several times or even tens of times that of the former. In terms of operating costs, the proportion of electricity consumption to vulnerable parts is high, so it is crucial to reduce operating costs. In the design of this dust removal process, we have made innovations in the following aspects compared to other similar equipment;
1. We design a soft connection between the dust collector outlet and the fan to prevent vibration caused by the high-speed operation of the fan; A silencer is designed at the outlet of the fan to reduce the noise generated by the high-speed operation of the fan;
2. For the convenience of maintenance and observation of the dust collector, we have designed a glass observation (maintenance) door at the bottom of the dust collector ash hopper; The system pipeline is connected by flanges between 4-6 meters, and there is a maintenance door designed around 5m; Facilitate observation of dust settling inside the pipeline and cleaning;
3. In response to the hydrophilic characteristics of wood dust, dust is prone to clumping under certain moisture content, which can cause blockage in the ash hopper of the dust collector. We have designed a vibrator in the ash hopper of the dust collector to assist in cleaning and reduce the need for manual assistance in cleaning;
4. The electrical control of the dust removal system and the ventilation and dust removal system require supporting fans and air compressors, and the drive requires a three-phase four wire power supply. The dust removal device needs to be equipped with one pulse controller for dust removal. The pulse controller is installed near the dust removal device, and the power supply of the control cabinet (box) is provided by the construction party. It is required to pull the cable to the main switch post inside the control cabinet, and provide a public grounding for easy ground wire connection.
5. In response to the high concentration of wood dust, we adopt a gradient airflow channel design for the dust collector, with uniform airflow distribution. Optimize the air flow organization design to avoid high-speed erosion and wear of local areas inside the dust collector, so that the compressed air for dust removal can evenly spray and filter all filter bags, improving the overall service life of the filter bags.