SURVIVAL THROUGH QUALITY
PRODUCT CENTER
-
Pulse dust collector
-
Mine dust collector
-
Boiler dust collector
-
Metallurgical dust collector
-
Carbon plant dust collector
-
Chemical dust collector
-
Rubber dust collector
-
Woodworking dust collector
-
Single machine dust collector
-
Static electricity Dust collector
-
Cyclone dust collector
-
Wet dust collector
-
Filter cartridge dust collector
-
Insert valve (gate valve)
-
Ventilation butterfly valve (cold air valve)
-
Spiral conveyor (auger)
-
Scraper conveyor
-
Dust humidifier
-
Bucket elevator
-
Ash discharge valve
-
Material Handling Equipment
-
Wet scrubber
-
Dust collector
-
Dust removal filter bag
-
Dust removal bag cage
-
Polishing platform
-
Waste gas treatment equipment
-
Electric control cabinet
-
Fan
-
Smoke welding machine
-
Liquid level switch
-
Dust removal filter element
-
Aeration cushion
-
Sweeper
-
Dust suppression device
-
Solenoid valve
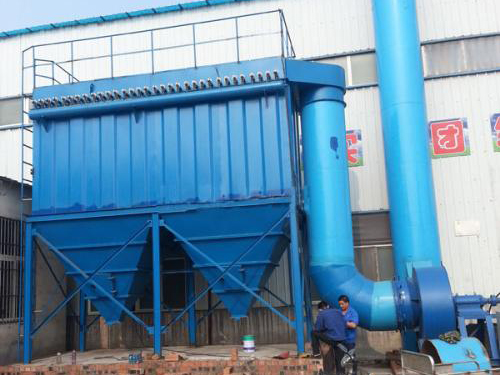
Dust collector in rubber refining workshop
During the feeding process of the internal mixer, material dust will be generated. A gas collection hood should be installed above the feeding port and connected to the bag filter. The collected dust will be collected by the bag filter, and the collected material will be recycled and reused. The capture efficiency of the bag filter is based on, and the exhaust gas is discharged through the exhaust pipe (15m), which can meet the emission standards. There are many dust generating equipment in the rubber refining workshop, which provides a safe operating environment and protects the physical and mental health of workers. Ventilation hoods should also be installed in areas with smoke and hot air, and they should be discharged outdoors or through chimneys through fans.
The selection of appropriate specifications of dust collectors and fans in the dust removal and ventilation design process of the rubber refining workshop is the key to whether the dust removal and ventilation can meet the design requirements, and it also determines the scale of investment and the cost of future use and maintenance. Our company has relevant technical personnel to design and produce ventilation and dust removal systems for many rubber factories, which have good dust removal effects, reasonable structures, and low operation and maintenance costs. The three prevention (,,) dust removal bags are widely used in the carbon black dust removal industry. The dust collectors in the rubber refining workshop of the rubber plant mainly include: bag dust collectors for the feeding device after the internal mixer, carbon black bag dust collectors, and tank dust collectors.
Design standard for dust collector in rubber refining workshop:
(1) The dust collector hood should be as close to the pollution source as possible without affecting the operation and maintenance of the mixer. When considering installation and maintenance conditions, a fully enclosed structure should be adopted to reduce the dust removal air volume. If it is not allowed to use a fully enclosed structure, it can be considered to add a soft barrier edge enclosed structure.
(2) The dust collector hood of the rubber refining machine should be fixed with a wind deflector in the middle of the hood opening as much as possible, without affecting installation and maintenance. Ventilation openings should be left around the hood outlet to reduce the cross-sectional area of the hood, increase wind speed or reduce air volume. Under the premise of constant wind speed, the percentage reduction in area is equal to the percentage reduction in air volume. For example, our factory uses a 1.5m x 0.8m square air hood to match the 110L internal mixer in Dalian Yunshan. A wind deflector is added at the suction hood opening, leaving a 120mm gap around it, reducing ventilation by 80%. This allows for the use of smaller fans and dust collectors to achieve similar ventilation and dust removal effects, saving users a lot of costs.
(3) Due to the presence of plastic bags, paper bags, or small rubber beans at the feeding ports of the unpacking machine, internal mixer, and small material feeding ports, if the air flow is too high, it is easy to suck the plastic bags or paper bags into the dust collector and attach them to the filter bag. It is difficult to remove them by using reverse blowing, which affects the dust removal effect. If entering the ash discharge screw or rotating ash discharge valve, these debris are likely to entangle on the screw or ash discharge valve blades, or even squeeze into the gap of the screw or ash discharge valve, causing malfunctions (which may occur during user use). Therefore, it is required to add steel plate mesh to the wind hoods in these areas, with a mesh diameter of about 8-10mm.
(4) Different specifications of suction hoods and dust collectors can be designed according to the on-site installation conditions of the user. The cross-sectional wind speed of the wind hood is generally set at 0.5-1.0m/s, and the maximum value is taken when the wind hood is far from the pollution source. If the wind hood is too far away from the pollution source due to installation reasons, the cross-sectional wind speed can be increased to around 2m/s.