SURVIVAL THROUGH QUALITY
PRODUCT CENTER
-
Pulse dust collector
-
Mine dust collector
-
Boiler dust collector
-
Metallurgical dust collector
-
Carbon plant dust collector
-
Chemical dust collector
-
Rubber dust collector
-
Woodworking dust collector
-
Single machine dust collector
-
Static electricity Dust collector
-
Cyclone dust collector
-
Wet dust collector
-
Filter cartridge dust collector
-
Insert valve (gate valve)
-
Ventilation butterfly valve (cold air valve)
-
Spiral conveyor (auger)
-
Scraper conveyor
-
Dust humidifier
-
Bucket elevator
-
Ash discharge valve
-
Material Handling Equipment
-
Wet scrubber
-
Dust collector
-
Dust removal filter bag
-
Dust removal bag cage
-
Polishing platform
-
Waste gas treatment equipment
-
Electric control cabinet
-
Fan
-
Smoke welding machine
-
Liquid level switch
-
Dust removal filter element
-
Aeration cushion
-
Sweeper
-
Dust suppression device
-
Solenoid valve
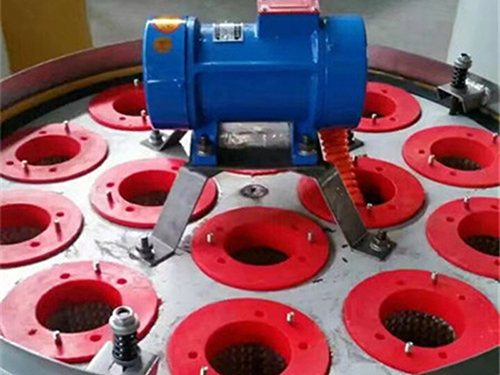
Pulse type top dust collector
The dust containing gas in the pulse top dust collector enters the dust collector box through the air inlet, and small dust particles are obstructed by the cloth bag on the outer wall of the cloth bag due to the obstruction of the dust air. The purified gas is discharged through the air outlet of the box on the cloth bag. As the usage time increases, the amount of dust adsorbed on the surface of the cloth bag increases, the breathability of the cloth bag weakens, and the resistance of the dust collector continues to increase. To ensure that the resistance of the dust collector is controlled within a limited range, a pulse control instrument sends a signal and sequentially opens the electromagnetic pulse valve, so that the compressed air in the air bag is sprayed from each nozzle of the blowing tube to the corresponding Venturi tube (called primary air). When the high-speed airflow passes through the Venturi tube, it induces several times more surrounding air (called secondary air) than the primary air to enter the cloth bag, causing rapid expansion between the cloth bags. Due to the rapid disappearance of the impact of the reverse pulse airflow, the cloth bag shrinks sharply, thus clearing the dust on the outer wall of the cloth bag. The falling dust enters the ash bin. [1]
Due to the fact that dust removal is carried out in turns through several sets of filter cartridges without cutting off the dusty air that needs to be treated, the processing capacity of the dust collector remains unchanged during the dust removal process.
The composition of the pulse top dust collector spraying system includes a compressed air bag connected to the pulse valve A end and a spraying pipe connected to the B end. The pulse valve backpressure control valve and control action are commanded by the control instrument. When there is no signal output from the control instrument, the movable iron core of the control valve seals the exhaust port, and the pulse valve is in a closed state. When the control instrument sends a signal, the control valve communicates the pulse back pressure chamber with the atmosphere, opens the pulse valve, and compressed air is sprayed into the Venturi tube through the small hole of the blowing pipe through the pulse valve, causing instantaneous positive pressure inside the filter bag and achieving dust cleaning.