SURVIVAL THROUGH QUALITY
PRODUCT CENTER
-
Pulse dust collector
-
Mine dust collector
-
Boiler dust collector
-
Metallurgical dust collector
-
Carbon plant dust collector
-
Chemical dust collector
-
Rubber dust collector
-
Woodworking dust collector
-
Single machine dust collector
-
Static electricity Dust collector
-
Cyclone dust collector
-
Wet dust collector
-
Filter cartridge dust collector
-
Insert valve (gate valve)
-
Ventilation butterfly valve (cold air valve)
-
Spiral conveyor (auger)
-
Scraper conveyor
-
Dust humidifier
-
Bucket elevator
-
Ash discharge valve
-
Material Handling Equipment
-
Wet scrubber
-
Dust collector
-
Dust removal filter bag
-
Dust removal bag cage
-
Polishing platform
-
Waste gas treatment equipment
-
Electric control cabinet
-
Fan
-
Smoke welding machine
-
Liquid level switch
-
Dust removal filter element
-
Aeration cushion
-
Sweeper
-
Dust suppression device
-
Solenoid valve
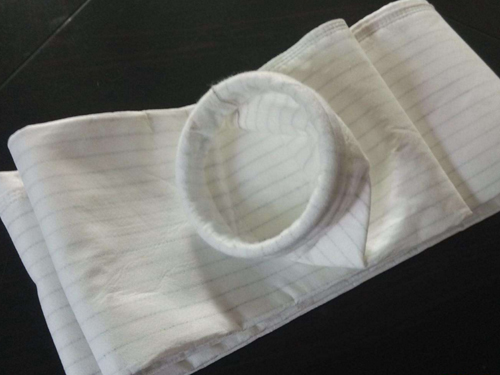
Polyester anti-static cloth bag
In addition to the process of producing ordinary needle punched felt dust removal cloth bags, polyester cloth bags also require the incorporation of conductive fiber yarn into the warp of the base fabric for producing needle punched felt, or the mixing of conductive fibers or conductive materials into chemical fibers. Used for dust removal and filtration of explosive industrial dust, dust removal bags are particularly suitable for dust collection in blast furnace gas, coal mill, cement plant coal mill, and other industries. It is currently an ideal choice for dust removal accessories.
When the concentration of industrial dust reaches a certain level (i.e. explosion), it is easy to cause explosions and fires when encountering factors such as electrostatic discharge sparks or external ignition. For example: flour dust, chemical dust, explosive dust, etc. In case of electrostatic discharge, there is a possibility of explosion in bag dust removal. If these dust particles need to be collected using cloth bags, it is required that the cloth bags themselves have functions. In addition to the production of ordinary needle punched felt technology, the production of filter materials also requires the addition of conductive fiber yarn in the warp yarn of the base fabric for producing needle punched felt or conductive fiber yarn in the concrete of chemical fibers.
After the concentration of general industrial dust reaches a certain level (i.e. explosion), it is easy to cause explosion and fire when encountering factors such as electrostatic discharge sparks or external ignition. In the dust removal system, the mutual friction, collision, peeling, and crushing of dust in pipelines, filter bags, and between dust can cause static electricity to be generated on the surface of dust and filter materials. When the surface of the filter material carries a certain amount of charge and cannot be released in a timely manner, it will form a high-voltage discharge and generate electric sparks, which may lead to dust explosions. There are two types of polyester needle punched felt dust removal cloth bags produced by our company: one is to incorporate copper permeable complex conductive yarn into the warp yarn of the needle punched felt base fabric, called stripes; Another method is to uniformly mix conductive fibers into chemical fibers, which is called blending. The needle punched felt filter bag has been tested by the department and has achieved ideal results in actual working conditions in many domestic blast furnace gas coal mills, cement plant coal mills, coal washing plants, woodworking dust collection systems, and flour factories, providing users with considerable economic benefits and receiving user evaluations.
The polyester bag is made of conductive fiber base fabric, with both sides of the base fabric needle punched with Dahua polyester or mixed with conductive fibers and Dahua polyester fibers. This filter material has good conductivity and high air permeability. After being treated with singeing, calendering, and microwave shaping, the cloth bag does not shrink at high temperatures in an instant. The ash facing surface is flat and smooth, with high strength and strong ability. It is a commonly used material suitable for filtering explosive dust.
Material: Polyester short fiber or mixed conductive fiber/conductive fabric or polyester fabric
Weight: > 500g/㎡
Thickness: 1.8mm
Meridional strength: > 1200N/5 × 20cm
Latitudinal strength: > 1400N/5 × 20cm
Meridian elongation: < 35%
Latitudinal elongation: < 35%
Breathability: 15-35m/ ㎡/min
Film covering: 2-5m/ ㎡/min
Operating temperature: < 130 ℃, instantaneous 150 ℃
Filtering wind speed: < 1.1m/min
Surface resistance: 4.8 × 109 Ω
Friction potential: 183V (average)
Post processing: singeing and pressing, microwave shaping